模具寿命指在保证制件质量的前提下,所能成形出的制件数。它包括反复刃磨和更换易损件,直至模具的主要部分更换所成形的合格制件总数。一般来说,压铸模具的失效,不外乎下列四种:
- 疲劳磨损
- 气蚀磨损与冲蚀磨损
- 断裂失效
- 塑性变形失效
本文将以两套造型几乎相同,但是加热配置设计不同的模具为例,从模具的破坏处反推可能的模具损害原因,再以铸造模拟制程软件 FLOW-3D 加以验证问题点。
问题描述
图一为两套造型类似的模具,在四万模次后发生了模具磨损的问题。图中A、B两处分别为模具上的两个滑块入子位置。图二为磨损状况放大图。
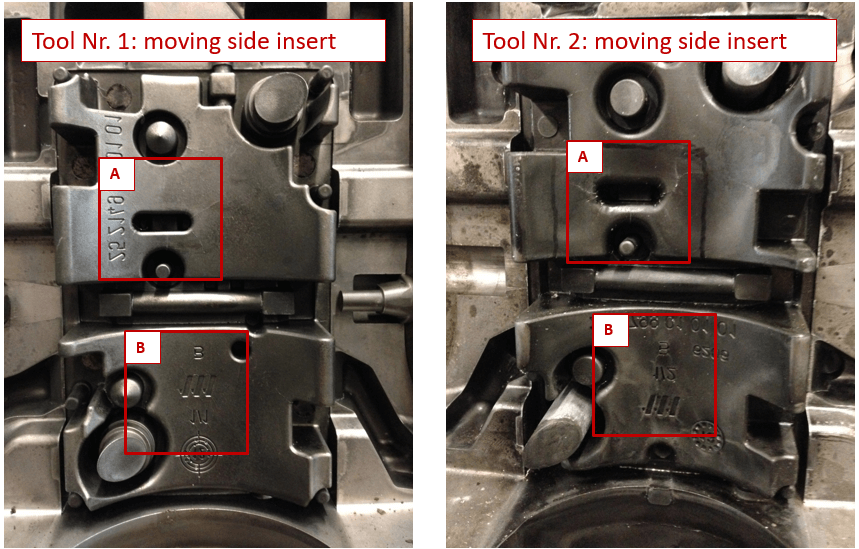

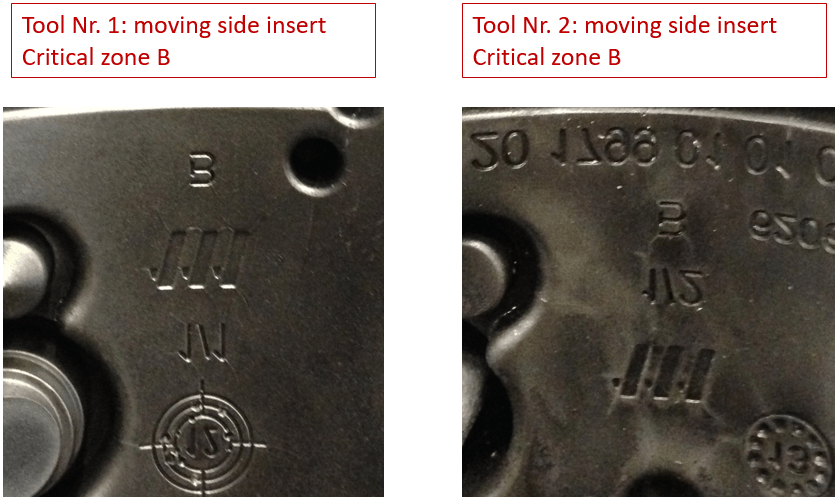
由于右侧模具(代号 Tool Nr.2)的磨损较左侧模具(代号 Tool Nr.1)相对严重许多,因此工程人员希望找出两者之间的差异原因,以作为日后模具设计修改的依据。
这两套模具材料均采用ADC-3,拉伸强度(Yield Strength)为1250 N/mm2,破坏强度为 1600 N/mm2。模具在 5000次成形时开始发生裂痕,疲劳破坏强度约为 850 N/mm2。
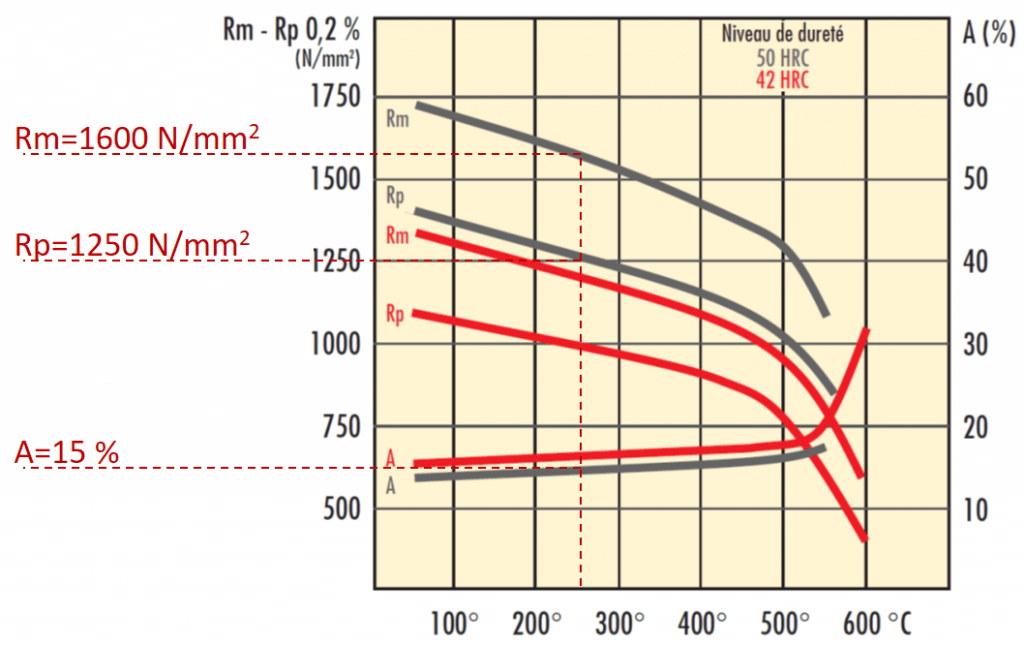
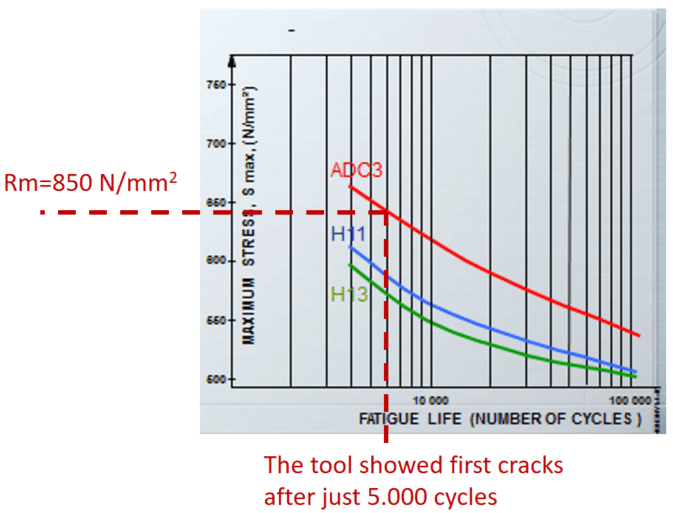
除了冷却设计之外,这两套模具的配置几乎完全相同。
在模具的操作侧及反操作侧各有一组滑块外,在地侧也有一组滑块(共三组滑块)。
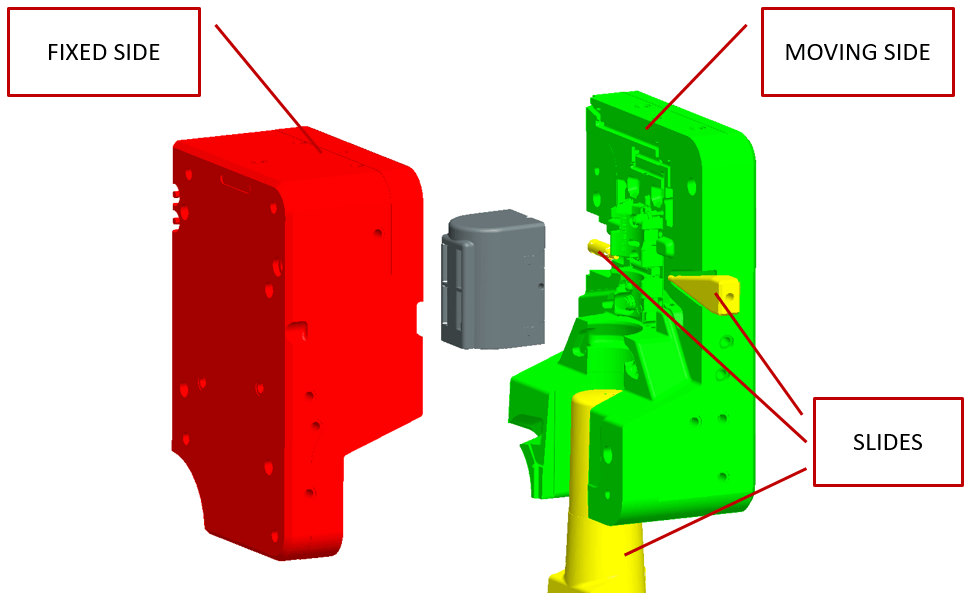
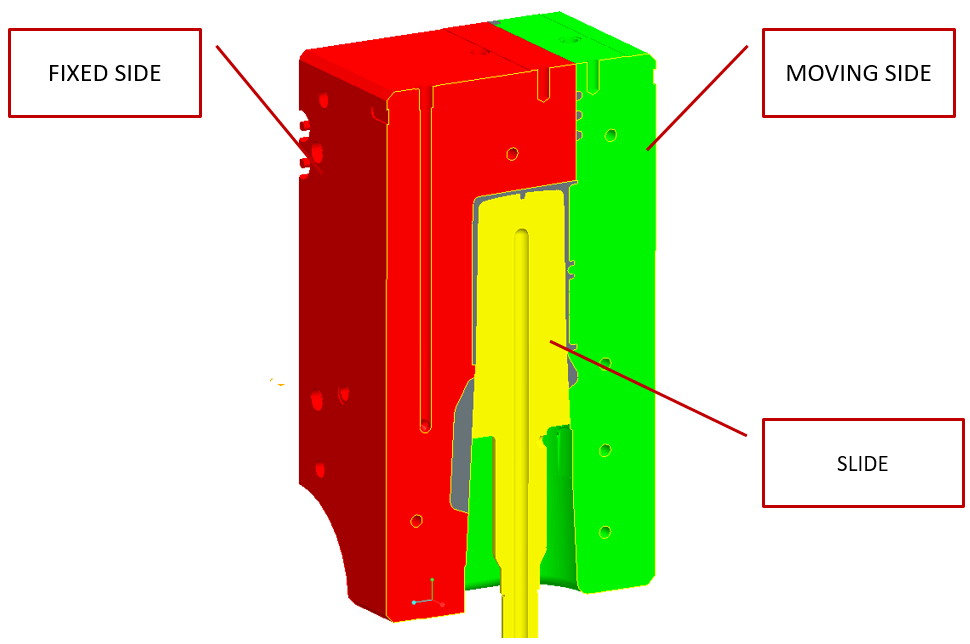
Fig4. 模具配置图
冷却系统配置差异
Tool Nr1 与 Tool Nr2 虽然模具配置类似,但是冷却管路的配置是不同的。相较于 Tool Nr1,Tool Nr2 因为造型多了两个凸块,因此在可动侧增额外增加了三只水路做局部冷却。
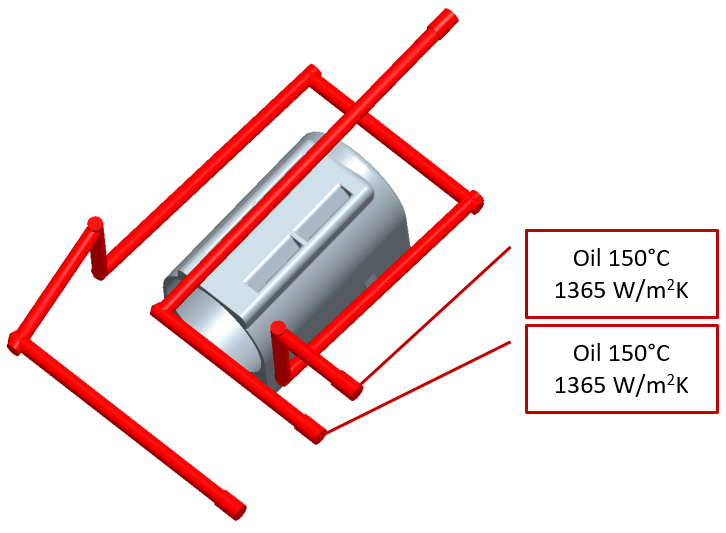
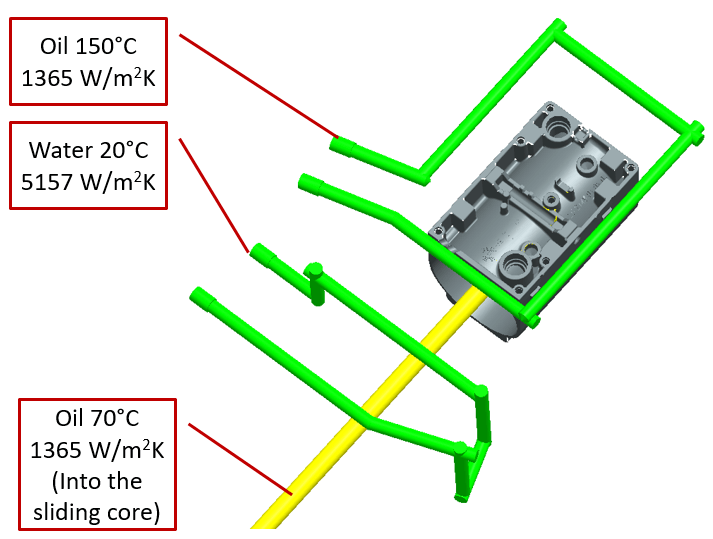
Fig5-1. Tool Nr1 冷却管路配置(左:固定侧, 右:可动侧)
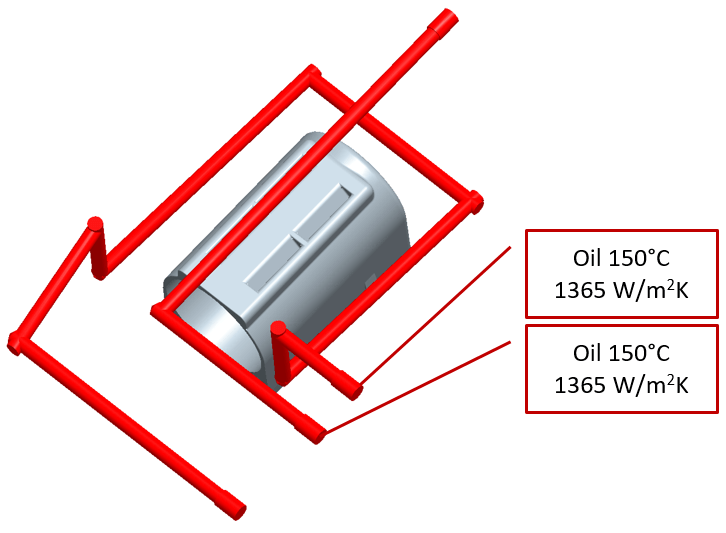
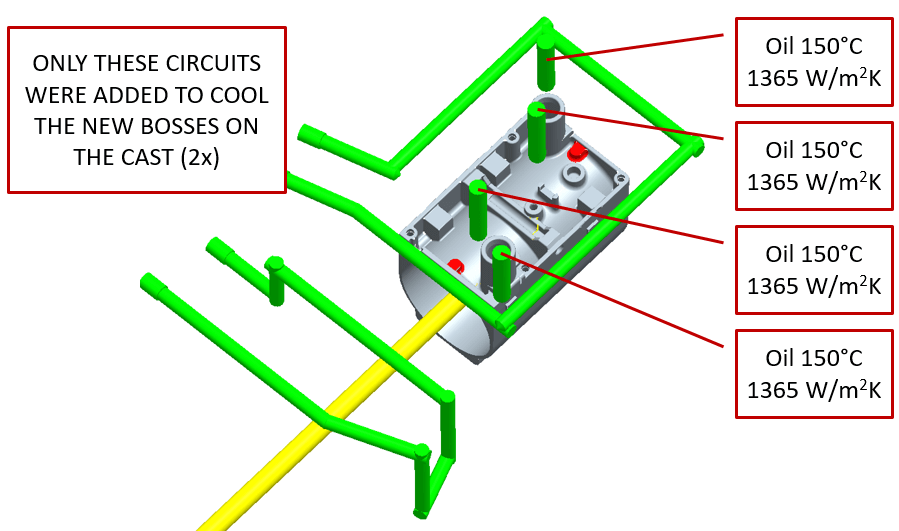
Fig5-2. Tool Nr2 冷却管路配置(左:固定侧, 右:可动侧)
Tool Nr2额外增加的三个冷却管路与成品面距离为 20mm,比标准设计 (15mm)多了 5mm。
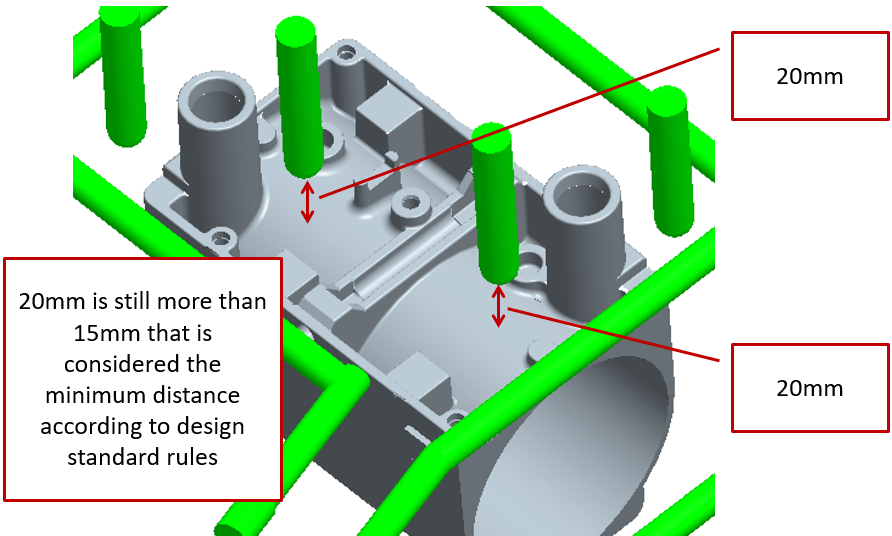
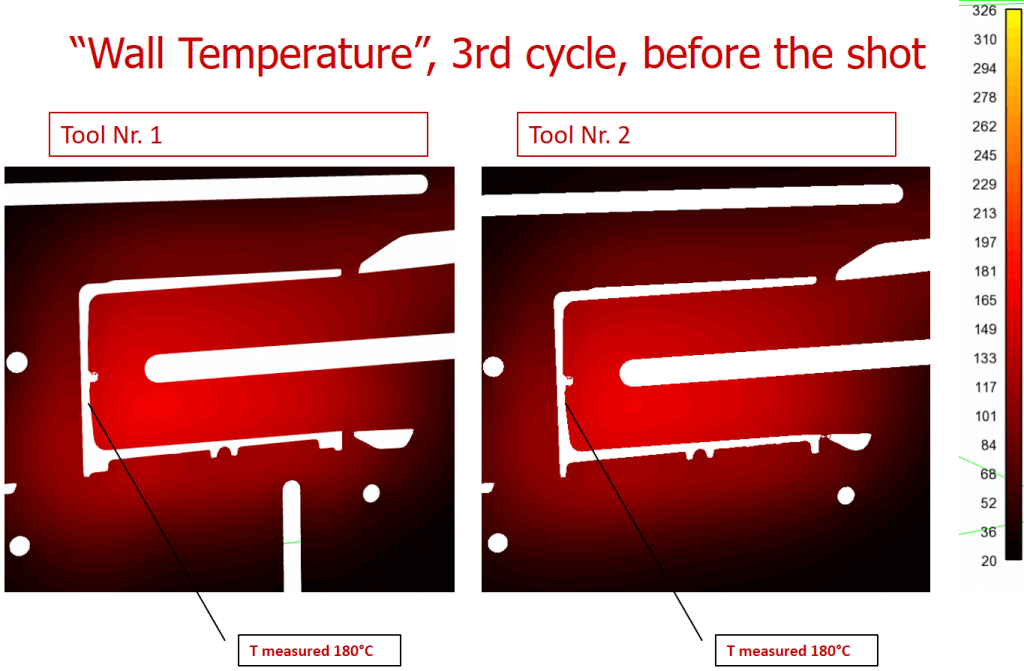
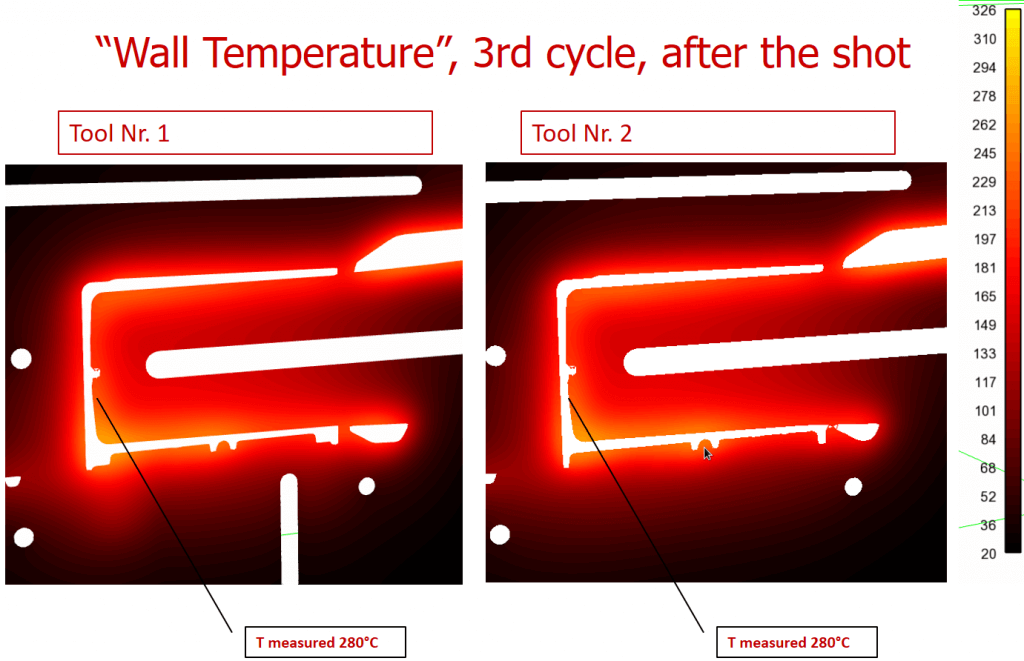
Fig8. 两组模具在第三次循环铸件成形前与成形后之温度分布差异
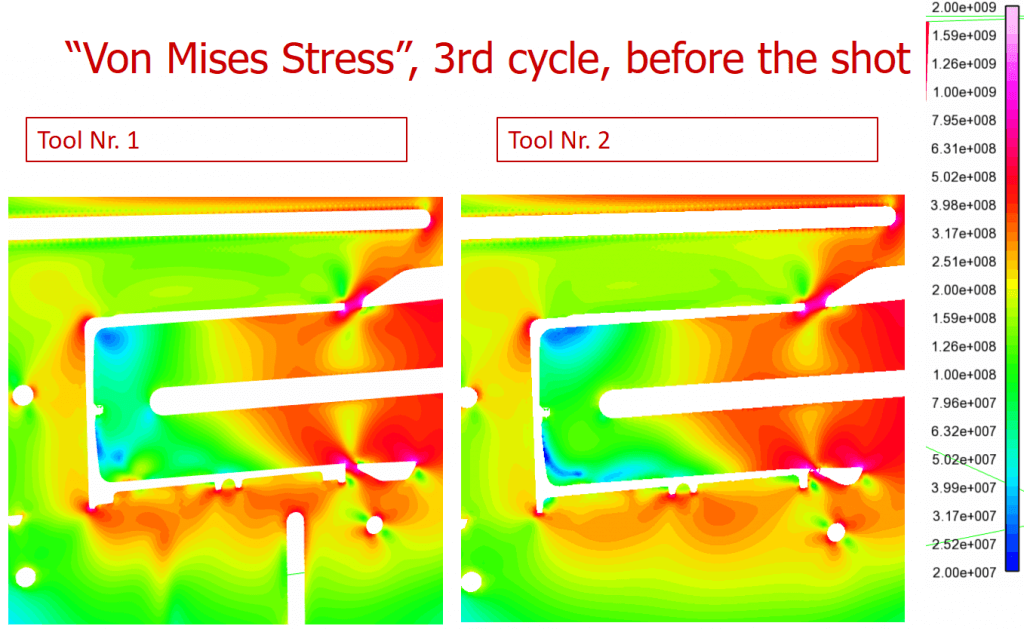
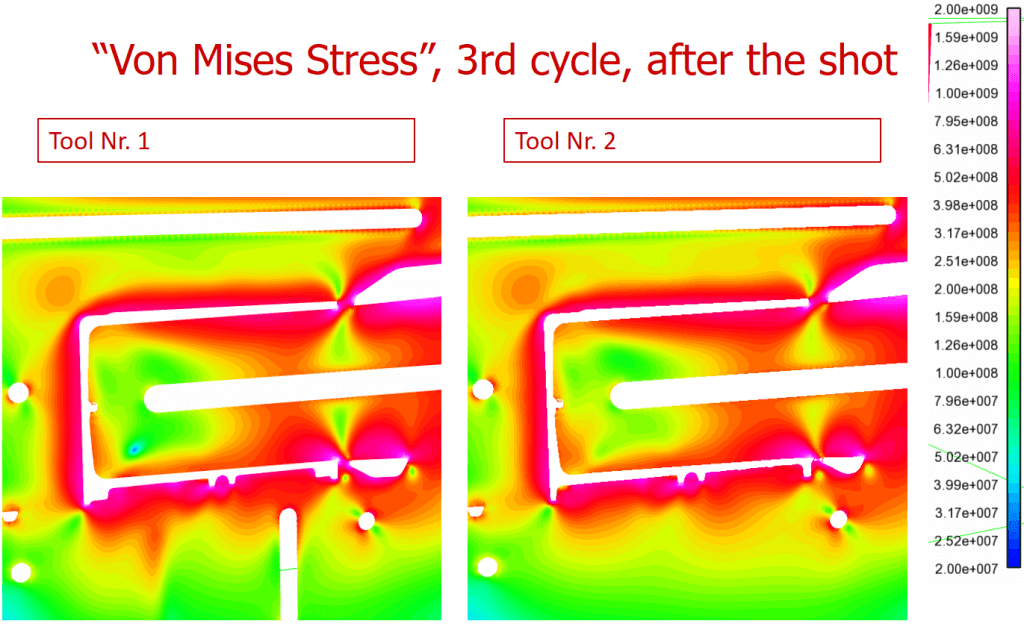
Fig9. 两组模具在第三次循环铸件成形前与成形后之热应力分布差异
根据模具热循环结果,可发现两套模具在特定区域的热应力集中现象相当严重,而这也正是滑块与铸件接触位置。
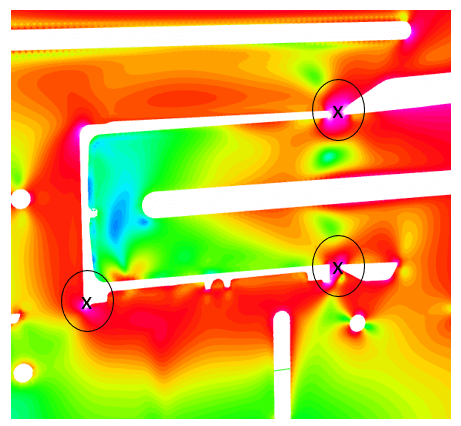
而这两套模具中,Tool Nr2 在模具热应力集中位置之数值又比 Tool Nr1来得大,表示该位置热应力集中现象更加严重。
本研究确认以FLOW-3D可追踪热应力集中现象,在适当的网格加密以及数值模拟下,可猜测模具发生破坏的原因并且预测破坏位置。至于破坏数值的大小,则需要取得更多的实验数据协助判定。