光学测量如何避免昂贵的精炼步骤
BOEHLERIT已在模具制造中使用光学3D测量。这导致精炼步骤减少。 在奥地利的硬质合金切削材料制造商中,质量保证从生产过程的开始就开始。公司自己的冲压工具部门使用Alicona 3D测量系统来优化印章。此外,InfiniteFocus 3D测量系统通过将开发时间减少了30%,使整个刀片制造过程更加经济。这使得更快地发布新产品成为可能。
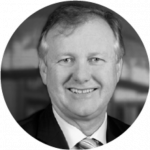
Gerhard Melcher, 段车削和铣削主管兼营销主管 “有了Alicona,我们已经在复杂几何形状的工具的制造上达到了更高的水平。得益于快速,高精度的测量技术,我们能够精确,经济地制造特殊工具。我们为使用其中一种工具感到自豪拥有Alicona的全球领先的测量系统-如果不是领先的测量系统。”
光学3D测量应用于模具制造
Boehlerit的质量保证以及质量和环境管理负责人Alfred Maier强调说:“在制造复杂的刀片几何时,关键在于正确的工具。” 他继续说,“制造刀片是一个费时且费时的过程。这意味着质量保证不能仅适用于成品刀具。”他描述了奥地利硬质合金刀具制造商的测量策略。阿尔弗雷德·迈耶(Alfred Maier)的质量保证理念始于模具制造制造过程的最开始。在施蒂里亚州Kapfenberg工厂,Boehlerit依靠其冲压工具部门的Alicona光学测量系统。Boehlerit的冶金,涂层技术和压制技术领域的专家使用Alicona’ 高分辨率3D测量系统InfiniteFocus结合电动旋转单元。这使他们可以优化印模和模具之间的间隙,并以全自动的可重复过程来测量嵌件的复杂几何形状。
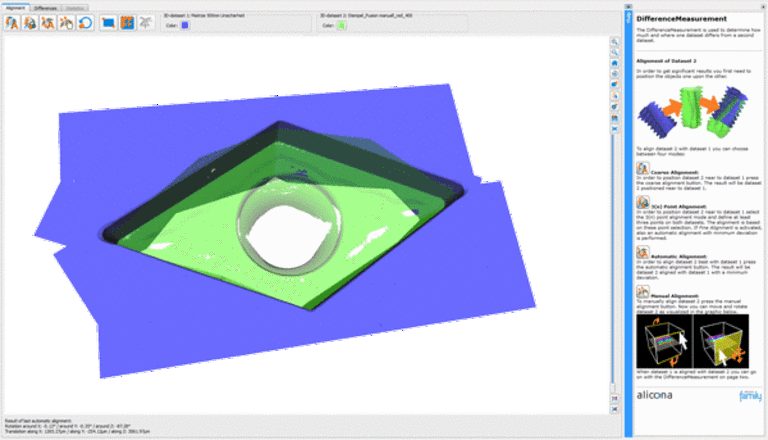
尺寸精度和表面粗糙度的测量
阿尔弗雷德·迈耶(Alfred Maier)解释说:“要接收精确制造的工具,邮票必须准确无误。因此,Boehlerit十分重视在自己的冲压工具部门为6000多种不同类型的嵌件制造理想的印模。通过确保压模和模具之间的间隙尽可能小来生产理想的压模,因为这样可以减少磨损。为此,Boehlerit使用InfiniteFocus系统测量对准的印模和模具,确定最佳间隙值。然后将光学高分辨率测量系统用于进一步的测量。Boehlerit验证在压制的原始零件上执行的后处理和校正步骤,以实现所需的尺寸精度和表面粗糙度。
减少后处理和提炼
自然,对于Boehlerit的质量保证,最佳和最经济的方案是是否几乎不需要甚至不需要后处理或修正,因为诸如研磨之类的精炼步骤很昂贵。在这方面,结合了电动旋转单元的InfiniteFocus系统已经为公司带来了回报。由于有了该系统,Boehlerit能够显着减少后处理,并且纠正步骤也变得更加高效。这缩短了准备进行批量生产的整体产品开发时间。阿尔弗雷德·迈耶(Alfred Maier)解释说:“过去,我们使用触觉测量设备来检查压制的原始零件。这些零件很快达到了极限,尤其是在测量复杂的几何形状时。我们今天生产的刀片不再具有直边。
将开发时间缩短了三分之一以上
Meier描述了光学计量学所取得的改进:“借助InfiniteFocus,我们能够更精确地制造复杂的几何形状,并且不需要进行矫正磨削。例如,我们能够大幅减少毛刺。” Boehlerit部门车削和铣削部门负责人兼营销负责人Gerhard Melcher用数字表示了这些进步:“我们过去的产品开发时间长达1.5年。得益于InfiniteFocus,我们能够缩短开发周期如今,尽管边缘几何形状越来越复杂,但我们的加工工具已准备就绪,可以在不到10个月的时间内推出。”
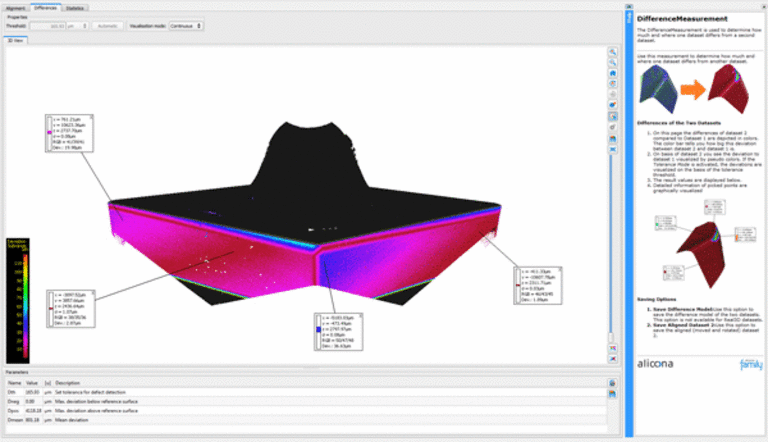
一个测量周期内所有相关的边缘几何形状
随着边缘几何形状的复杂性增加,质量保证和测量系统的要求也越来越高。这对负责质量保证的人员造成巨大压力。阿尔弗雷德·迈耶(Alfred Maier)解释说:“我们希望工作迅速,不要让生产等待。同时,测量必须准确,有效且可重复。” Boehlerit与Alicona一起找到了满足这些要求的理想合作伙伴。质量保证部门从全自动电动旋转单元中获得了巨大收益。Boehlerit的测量技术人员Markus Peihser描述了这些优点:“旋转单元使我能够在一个测量周期内自动测量所有相关的几何形状和边缘参数。无需在夹具中重新放置零件。”
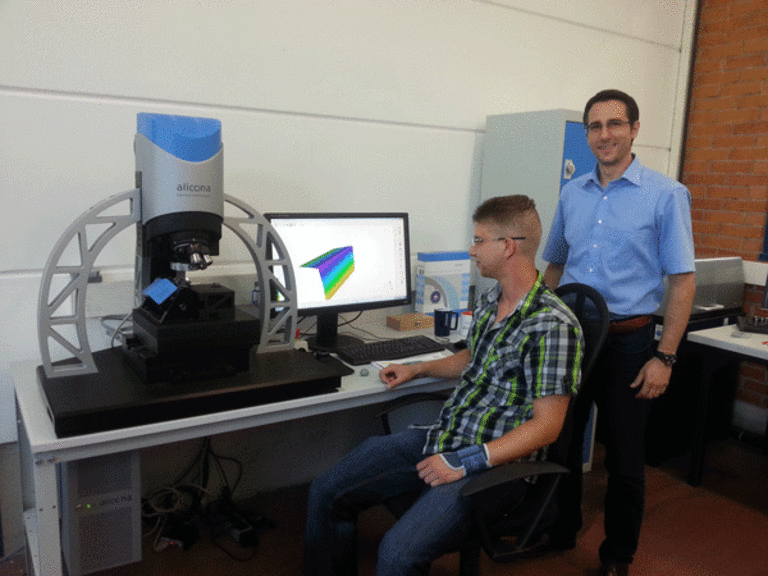
测量的高重复性
质量保证的另一个功能是系统导入外部数据集的功能。这些使自动测量尺寸成为可能。此外,偏差也以图形方式显示。Peihser指出:“尺寸过大和尺寸过大也可以通过颜色代码进行可视化。因此,我们可以更快地发现故障,避免耗时的校正,并从整体上加快了整个过程。” InfiniteFocus 3D测量的高可重复性已成为Boehlerit提高效率的另一个重要因素。市场主管Gerhard Melcher:“我们还是其他工具制造商的供应商和开发合作伙伴。我们的客户需要广泛的文档和测量的可重复性。
Boehlerit使用Alicona系统执行以下测量:
- 压模和模具之间的间隙的测量
- 3D测量压制零件的几何形状
- 校正过程和后处理(如研磨)的数值验证
- 自动测量形状偏差
- 使用Real3D技术对刀片的几何形状进行全面测量