摘要
目前,压铸铝合金零件已经被广泛应用到汽车、航空航天和电子工业等领域中。用铝合金零件代替钢制零部件能够实现40%~50%的减重,这有利于降低能耗,是实现节能减排的重要途径。因此,越来越多的汽车结构件采用铝合金材质,以减轻重量,但其复杂的结构及高受力要求对压铸工艺提出了挑战。汽车的许多结构件多为薄壁壳体类零件。研究表明,当铸件的壁厚小于4mm时,液态金属表面张力引起的拉普拉斯力会严重影响充型液体的流动状态,同时粘滞力的作用也凸显,这会导致薄壁零件在模具型腔中充型困难。压铸技术是使金属液在压力下充填型腔,这不仅能有效解决充型的难题,而且能使金属液快速凝固,细化合金组织,得到强度更高的合金零件。
由于这些壳体零件一般形状比较复杂,局部壁厚不均匀,因此金属在模具型腔中的流动过程也较为复杂,并且由于不同铸型材料、金属材料的性质不同,也会导致对铸件质量难以把握。如今,随着计算机技术的发展,数值模拟软件能越来越准确地反映金属液在压铸模具的流动过程,并且能够准确预测铸件缺陷产生部位。因此,首先利用数值模拟软件预先进行充型及凝固过程的模拟,然后根据模拟结果设计及优化压铸工艺,分析零件品质,是一种高效且节省成本的方法。
本文涉及的汽车结构件减震塔,属于大型、复杂铝合金压铸件。运用FLOW-3D数值模拟软件进行模拟,指导设计该零件的压铸工艺方案,验证了零件制造工艺的合理性和可行性。根据模拟结果对工艺方案进行改进,最终获得高质量的压铸件,提高了零件的生产效率,降低生产成本。
01 减震塔结构分析
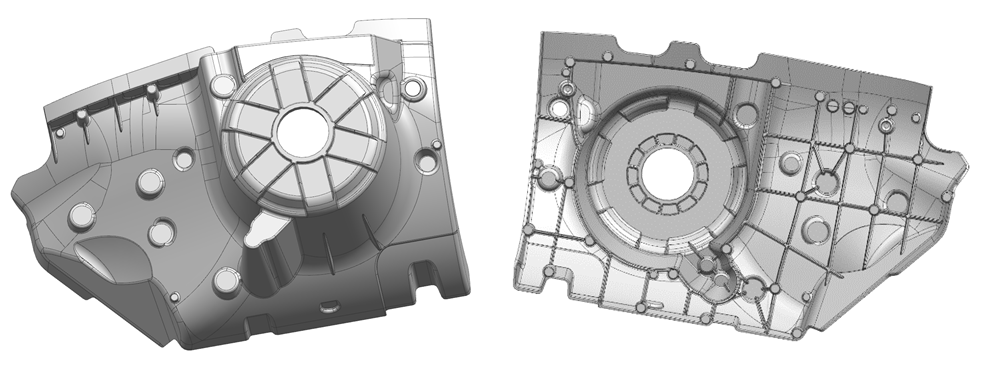
图1 某减震塔三维实体造型
图1 为某减震塔三维实体造型示意图。铸件最大轮廓尺寸为530mm*345mm*313mm,主体平均壁厚为3mm。铸件结构复杂,整个壳体呈弧形,表面设计有纵横交错的加强筋,以提高零件的整体强度;局部存在较多近圆柱形凸台,最大高度达到20mm,使铸件各部位壁厚差异较大。在铸件一侧存在一尺寸较大的凸起结构,与铸件壳体部位高度差达到195mm。该减震塔用A380铝合金压铸成形,铸件净重2.9kg。
02 浇注系统和排气槽、溢流槽的设计
2.1浇铸系统设计
浇注系统是金属液在压力下充填型腔的通道,是控制金属液充填型腔的速度、时间以及流动状态的重要部分。因此,设计合理的浇注系统是获得高质量压铸件的重要环节。根据铸件特征,选取铸件轮廓尺寸面积最大处作为分型面,便于零件脱模。为减小压铸过程开始阶段的卷气程度,在零件长度方向上选取形状结构较为平直的一侧设置内浇口。根据经验公式(1)计算内浇口截面面积:
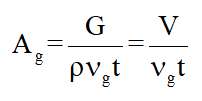
式中,V为零件及溢流、排气系统总体积(溢流、排气系统体积按照零件体积50%计算),为1157422mm3;νg为金属液在内浇口处速度,根据设计手册,铝合金在内浇口处的充填速度为20~60m/s,取值40m/s;t为金属液充填型腔的时间,其推荐值由平均壁厚决定。根据经验公式(2)计算平均壁厚:
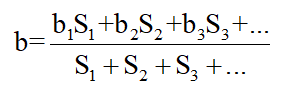
式中,b1、b2、b3…为铸件某个部位的壁厚(mm),S1、S2、S3…是壁厚为b1、b2、b3…部位的面积(mm2)。计算得到该减震塔平均壁厚为3mm,型腔充填时间推荐值为0.05~0.10s,取值0.07s。由此计算得到的内浇口截面面积Ag为391.87mm2;根据设计手册,内浇口厚度T取值1.5mm,内浇口总宽度L=Ag/T=261.25mm。压铸机为卧式冷室压铸机,横浇道截面积为Ar=(3~4)Ag=1371.545mm2,横浇道厚度D=(8~10)T=15mm;横浇道选用金属液热量损失小、且加工方便的常见的扁梯形。根据压铸机压室尺寸,直浇道直径(压室直径)为120mm。利用计算得到的直浇道、横浇道以及内浇口的参数,设计了该减震塔零件的浇铸系统,如图2 所示。
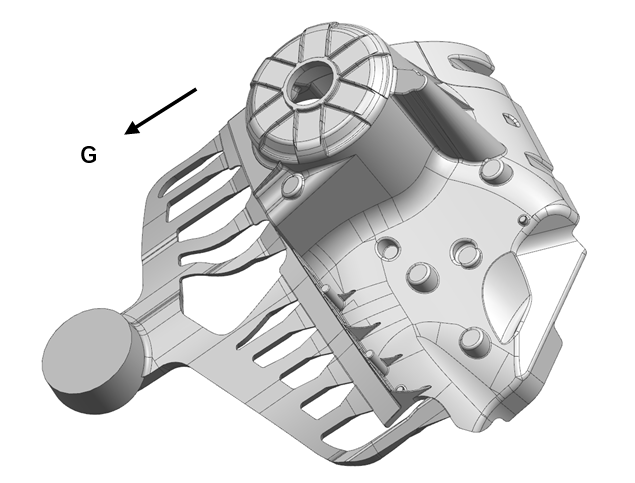
2.2 溢流槽、排气槽设计
溢流槽用于储存液-气界面前端混有气体和涂料残渣的冷污金属液,与排气槽配合,能够迅速引出型腔内的其气体,减小充型过程中卷气的发生,同时也能转移缩孔、缩松、涡流裹气和产生冷隔的部位。但是,要发挥溢流槽的作用,溢流必须根据金属液在型腔中的流动特征,在合理位置接受前沿冷污金属液并将其保留在溢流槽中,因此,溢流槽也需要合适的尺寸。既不能过大也不过小,过大会导致废料增多,增加成本;过小会导致溢流槽不能接受全部的冷污金属,而降低铸件质量。因此,先对在Flow-3D流模分析系统中设计好浇注系统的零件先进行数值模拟,然后根据金属液的流动特征确定合适的溢流系统是一种高效的设计手段。
根据实际的压铸工艺参数设定模拟参数,金属液先在慢压射速度0.6m/s下进入横浇道和内浇口,当金属液充满所有内浇口后,压射速度提高到5m/s,即让金属液在快速下充填型腔。
.png)
.png)
图3 带浇注系统模拟结果:温度场及卷气情况
图3 Flow-3D给出了金属液在充型过程中不同时间点的金属液的温度及卷气情况。可以看出,设计的浇注系统能够实现金属液较为平稳地充填型腔。在零件左侧存在两个圆形结构,根据充型过程的模拟,可以看到金属液在充填此处时容易产生涡流现象,从而造成卷气量增大。因此,应在圆形结构两侧设计溢流槽,以使卷气部分的金属液被排出型腔,进入溢流槽。根据温度场及卷气特征可以看到,在零件右侧存在较大面积的温度较低的金属液,并且由边缘向里延伸的方向,存在不同程度的卷气现象,如图3(c)中圈出的部位。对应图1 所示的减震塔结构可以看出,图中圈出部位结构较为复杂,金属液经最右侧的内浇口进入型腔后先直接冲击存在一定角度的型腔壁,受阻后金属液回流充填零件最右侧的部位,因此造成气体的大量卷入,这一点可以从金属液开始进入型腔的图中可以看出(图3(a))。零件由下至上依次充型,在金属液最后充填的零件上部存在大量温度较低且卷气严重的金属液,应当在此处设置足够多的溢流槽来接受这些金属液,以获得高质量铸件。
根据Flow-3D模拟结果,在某些部位的温度低、卷气量大的金属液较多,应当设计具有足够容积的溢流槽,但是过大的溢流槽又易导致金属液倒流,因此在这些部位设置多个单独的溢流槽并设置薄的连接肋以保证其强度。溢流槽主要采用便于加工的梯形溢流槽,在局部卷气严重的部位适当增加溢流槽容积并根据流动特征对形状进行小幅度修改(如图3(c)圈出部位)。根据设计手册,排气槽的截面积设置为内浇口截面积的30%。设计好的溢流槽及排气槽如图4所示。
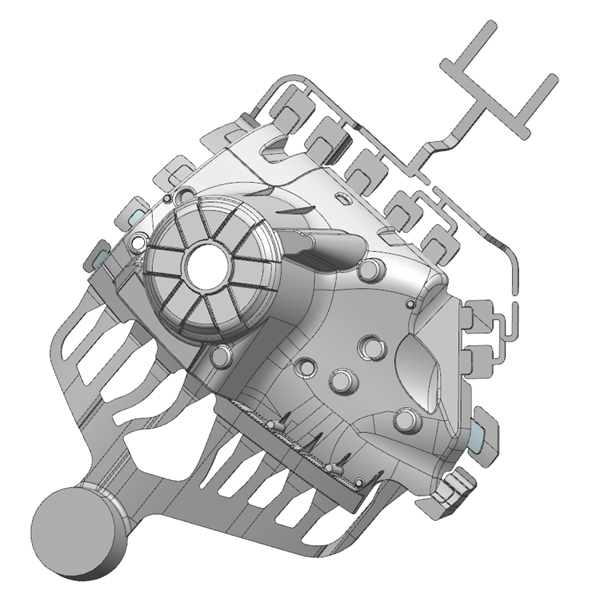
03 模拟分析及工艺优化
.png)
.png)
图5 带浇注系统和溢流槽、排气槽的模拟结果:温度场及卷气情况
图5 为金属液在带有浇注系统以及溢流槽、排气槽的压铸模具中的充型过程。可以看出,在金属液充型过程中,位于液-气界面前沿的温度较低、卷气严重的部分金属液全部进入设计好的溢流槽中,金属液充满型腔后(图5(d)),留在零件内部的气体量极少。因此,设计的溢流槽、排气槽适用于该减震塔零件的压铸工艺。
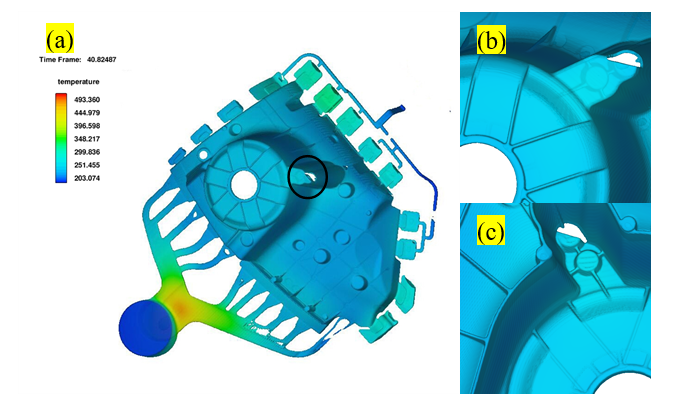
(a)完全凝固;(b)凸起结构上部放大图-凸面;(c)凸起结构上部放大图-凹面
图6 为Flow-3D所模拟出的金属液完全凝固后所得铸件的形状。可以看到,在减震塔零件中的凸起结构上部存在一较大的孔洞缺陷,观察其局部放大图可以发现,在该处存在两个尺寸较大的近圆柱形凸台,高度达到20mm。在凝固过程中,这一厚大部位凝固速度较慢,会发生补缩现象,形成孔洞。
对此,采取局部激冷的方法加快该部位的凝固速度,以获得致密的铸件。在该处的模具上加入激冷铜块以达到激冷的目的,其模拟结果如图7 所示,得到内部致密无孔松的健全铸件。最后采用该工艺实际生产出合格的铝合金减震塔零件,成品率达到90%以上。若通过控制模具温度等其他条件,成品率有望进一步提高。
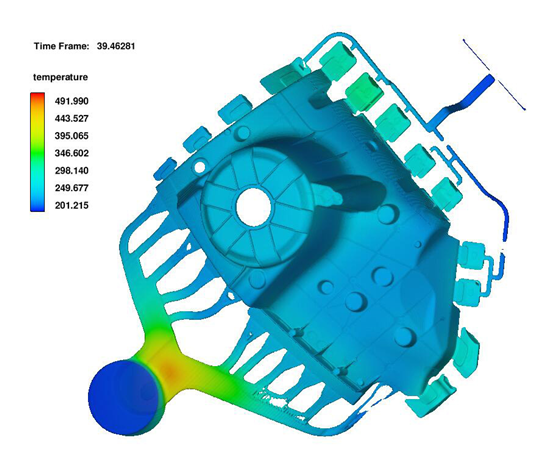
04 结论
- 设计、优选出大型、复杂汽车结构件——铝合金减震塔的压铸浇注系统及溢流和排气系统。
- 利用Flow-3D数值模拟方法分析了减震塔零件的卷气发生部位和区域,预测了压铸缺陷的种类及位置,以此为基础更改了浇注系统的设计。
- 在壁厚尺寸较大圆形结构处容易发生卷气现象和缩孔缺陷,采用局部激冷方法等工艺措施,消除了缺陷,获得整体质量良好的铝合金减震塔压铸件。
作者:
周林东、杨雄、王春涛,吕书林、张靖、吴树森
宁波合力模具科技股份有限公司,宁波;华中科技大学材料成形与模具技术国家重点实验室,武汉