齿轮齿面波纹度的光学三维测量
齿侧的波纹会在汽车内部引起不愉快的噪音。本田公司采用高分辨率和基于面积的测量技术,成功地将波纹度与侧面粗糙度进行了分离和量化。通过应用聚焦变化和频率分析方法,研究开发小组能够识别并成功地减少干扰噪声。
“我们以前使用的系统不再满足我们的要求。使用InfiniteFocus,我们测量得更快,获得更多有意义的信息。我们变得更有效率了!”Naoto Syukuma,本田动力总成样机部
优化准双曲面齿轮制造工艺
现代驾驶的舒适性和汽车内部的高噪音水平是一对矛盾。对于汽车工业来说,这意味着要避免NVH现象(“噪音、振动、刺耳”)。干扰噪音可能有他们的原因在变速箱的动力系统。通常,它们可以追溯到齿轮齿侧的波浪度。这就是为什么本田使用光学三维测量系统来识别和测量侧面的波纹度,使全球汽车制造商能够优化准双曲面齿轮的制造工艺,从而消除不必要的齿轮噪音。
在低噪声水平方面,准双曲面齿轮特别具有挑战性,因为它们是高频的,因此往往会传递振动和声音辐射,从而导致车辆内部的噪声。为了找到齿轮噪音的来源,本田使用了alicona光学三维扫描仪高分辨率测量仪器InfiniteFocus。形状和粗糙度测量系统是汽车集团的理想解决方案,其原因有:一方面,它还测量了陡峭侧面的高分辨率;另一方面,它允许基于密集、高分辨率和区域三维数据的粗糙度和波纹度的滤波。
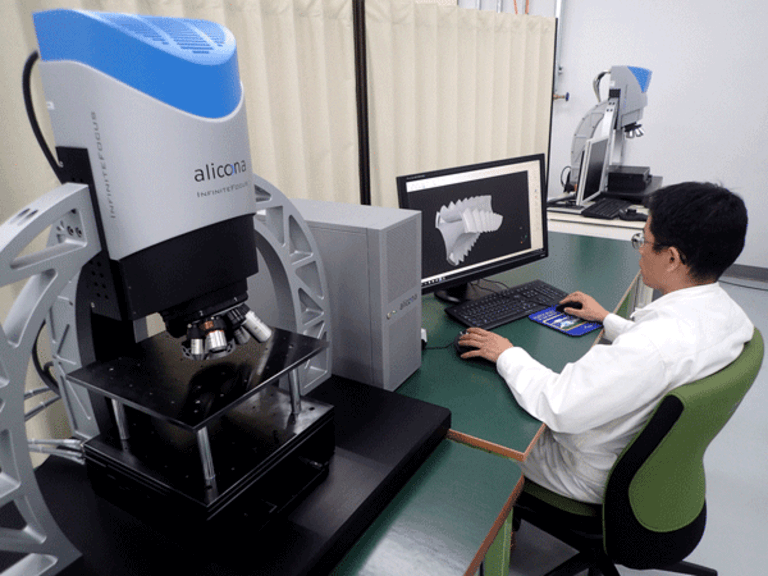
滤波粗糙度和波纹度
齿轮齿面波纹度测量面临的最大挑战之一是如何滤除表面的波纹度和粗糙度。对于本田来说,传统的2D成像技术并没有带来所要求的结果。波纹度往往是由铣刀等刀具标记叠加而成的,这使得将它们与粗糙度完全隔离起来是很有挑战性的。二维表面轮廓测量方法或触觉测量系统只捕捉单轮廓线,仅部分适用于这一目的。光学,基于面积的三维测量系统InfiniteFocus提供了更多的可能性。动力总成原型部的Naoto Syukuma解释道:“Ra值不足以验证侧面的真实表面状态,因为它们只捕捉单轮廓线。另一方面,基于面积的sa值,我们可以通过各种滤波方法将表面特征映射到整个表面上,然后将它们与波纹完全隔离开来。”这一分析的结果使本田能够适应准双曲面齿轮的制造工艺,从而有助于防止低档齿轮生产中的负面噪音发展。
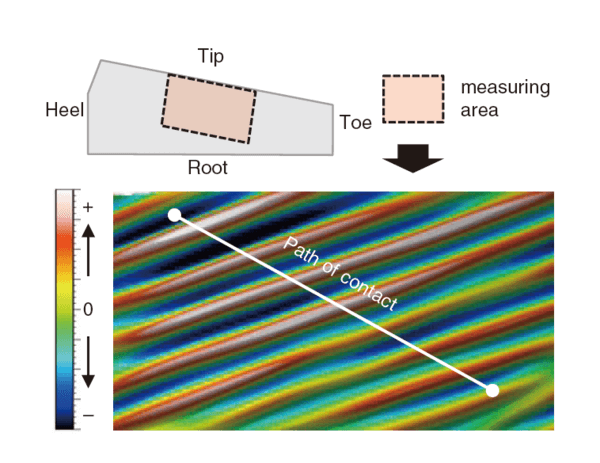
更快地测量陡峭的侧翼
本田说,高分辨率和可重复的测量,即使很难获得几何形状,如陡峭的侧翼,也是另一个将InfiniteFocus 3D显微形貌与粗糙度光学轮廓仪与其他计量供应商区别开来的基准。这就是Naoto Syukushima所称的对新测量系统的最初需求:“与Bruker Alicona的合作始于我们正在寻找一种也能测量陡峭侧翼的测量装置。”他接着说:“我们以前使用的系统已经不能满足我们的要求了。”使用InfiniteFocus,我们测量得更快,获得更多有意义的信息。“我们变得更有效率了!”本田说,其他方面也促成了这种效率的提高,包括3D测量系统的高用户友好性,用于快速和容易识别磨损的3D颜色报告,以及具有不同表面光洁度的侧翼的高测量性能。后者是由于磨损或不同的磨损阶段以及侧翼相关的不同反射特性。Syukuma提到了另一个好处:“我们的部件通常测量250 mm x 250 mm。”我们测试过的其他测量系统不能用于这个测量体积。
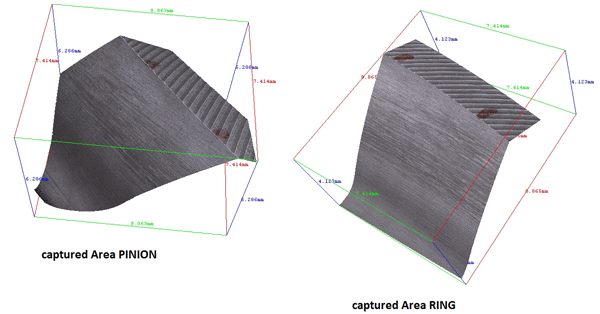
对于本田来说,有一个更决定性的因素,InfiniteFocus 3D测量系统提供了成功实现波浪度分析的条件。“我们可以输出3D,然后应用我们自己的分析程序。在我们的例子中,这些是频率分析方法。”因此,本田在齿轮侧翼波浪度的量化方面建立了一个新的标准。这一过程的专利证明了这一部门的重大影响和领导作用。